They were somewhat larger
than the official balls used, and livelier, using strands
of shoe rubber for the core.
The balls had a four piece
cover all equal, with each
point of the cover meeting, and
sewn together. Like quartered
Orange peels. (we'll get to that
later)
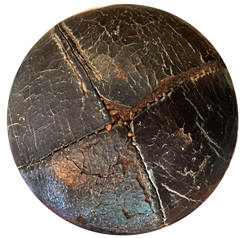
It was also common for a kid to unravel their mother's woolen stockings for
winding a ball, then go to the
village shoemaker and get him
to cut out with his knife, four
pieces of leather to sew on for
a cover. Waxed ends were used
to sew the four pieces of
leather on the ball. The boy
that had a pull with the
shoemaker and could get him to
sew the cover on was the most
popular boy in that section of
the country.
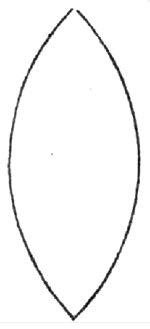
The illustration
to the left shows the shape of
one of the quarters used for
the cover which today is
commonly referred to as a Lemon
Peel baseball. But expert ball
manufactures back in the day
declared that it was first
suggested by the quartering of
an orange, which makes more
sense as, no matter how you
quarter a lemon you will not be
left with four pieces to sew
together to form a ball. An
orange is round. I think we
should revisit the naming of
these balls and change it to
Orange Peel baseballs.
The two piece figure-eight covers like
we use today were first used
around 1858. By 1870 the four
piece "Orange Peel" baseball is
talked about as a relic from
the past, in the "old days."
One line of balls made for boys
called the "Boss" ball,
featured a "four piece cover"
in the 1896 Spading catalog. Up
until the 1860's the Orange
peel balls could have been made
by any business that worked in
leather products. Shoe Maker's,
Saddle maker's and even a Sail
maker named Harry Ross, maker
of the "Ross" Ball.
History fails to
attribute the inventor of the
two piece “figure 8” cover.
Some historians claim it was
first developed by a
shoemaker’s son named Ellis
Drake, who supposedly put the
design together with some of
his father’s scrap leather in
an effort to create a more
resilient cover. Others,
including Al Reach, give credit
to Colonel William A. Cutler,
who may have invented
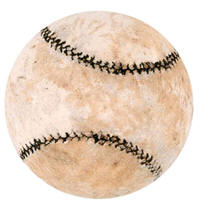
the
familiar stitching in 1858 and
sold it to one of the first
baseball manufacturers, Harwood
& Sons. (1885 accounts by Al
Reach to the left)
The following accounts are
excerpts taken from an 1891
baseball manufacture that was "building Base Balls" with
figure 8 covers.
The making of a league ball was a most careful and skillful job, and it
required good judgment to
follow accurately the league
rules as to measure and weight
while the ball is in process of
being made. Working by a window
for light, beginning the
manufacturing of a ball the
workman takes from an old peach
basket full of rubber spheres
one of the little globes. It is
the nucleolus of the ball,
today we call it the "pill."
For many years the early balls
were made with rubber balls
imported from England. The
English influence is also
noticeable as some balls are
sewn similar to cricket balls.
With the rubber ball in his left hand the workman holds it at the ends of
his fingers, and taking an end
of blue woolen yarn (the same
used to make mothers stockings)
he winds it on the ball with a
motion of his right hand so
rapidly that you cannot follow
it, while with his left hand,
as the ball grows larger, he
turns it so slowly one way and
another that the ball can
scarcely be seen to revolve. As
the ball grows larger it is
worked down from the finger
slips into the hollow of the
hand.
Now the workman uses a standard cup shaped hollow. Every minute or
sometimes every few seconds, he
puts the growing ball on the
standard and with a wooden
mallet, flat and rather wide
and short (sort of like a short
cricket bat) beats the ball,
turning it about in every way
as he hammers it. To make the
ball more solid the yarn is
dampened. When the desired
circumference is reached he is
done.
The covers are cut by using a steel die, and by boys working at nothing
else all day but with a die and
a mallet over a bench and
leather. Before the cover is
placed on the ball the leather
is put into a tub of water. The
leather must be wet through, so
that when it dries it will be
as tight as the bark on a tree
and as hard as iron. The
workman fits the pieces
together on the ball so the
edges meet, and with a
three-cornered needle similar
to that used by glovers, and
threaded with Irish linen
thread, he begins anywhere on
the seam, and sews rapidly
around until he has made the
circuit of the sphere.
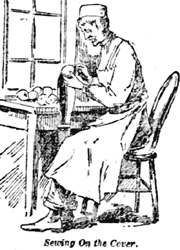
The chunk is laid
away to dry for several weeks.
When it is dried, a worker
winds the horsehide covered
ball with blue again until it
approaches the regulation size.
Then comes the last winding
with camels hair thread,
imported for the purpose. The
thread is dampened and it winds
far more tightly around the
ball than the finest silk. The
ponding of the ball is
continued until it is supposed
to be heavy enough and large
enough. To make sure that the
rules are being observed, the
workman from time to time puts
the ball into a scale,
something like a scale for
weighing letters.
The final process is putting on
the last cover. It is necessary
that the cover is dampened so
as to stretch on tightly, but
not too tightly. The sewing is
done with white Irish flax
linen. After sewing on the
cover there remains only the
wrapping of the ball in tissue
paper and afterwards tinfoil,
and finally the packing of it
in a stout paper which it
comfortably fits.